شما در حال خواندن انبارها هستید. این درس مربوط به مجموعه طرحریزی است.
انبارها محلی برای نگهداری اقلام مختلف مثل محصولات، مواد اولیه، قطعات نیمساخته، حاملهای انرژی، قطعات مصرفی ماشینآلات، لوازم اداری و مواد بهداشتی هستند. محل قرارگیری انبارها و لیاوت آنها روی هزینههای حملونقل، استفادهی بهینهتر از فضا، کاهش هزینهها و افزایش راندمان مؤثر است.
بحث انبارها میتواند بسیار مفصل باشد و حوزههای مختلفی را در بر بگیرد. مثلاً برای بهبود عملیات انبارداری، مناسب است که از یک سیستم کدگذاری برای نامگذاری قطعات استفاده و ترتیبی برای ردیابی محل قرارگیری آنها پیشبینی کنیم. به طور کلی استانداردهای متعددی در مورد انبارها وجود دارد که شامل ملاحظات و قواعد مختفی هستند. گاهی جابهجایی مواد به تجهیزات خاصی نیاز دارد و بحث انتخاب یا طراحی آنها مطرح میشود. مثلاً شاید تولیدکنندهای تصمیم بگیرد که یک سیستم مکانیزه برای قراردادن مواد در قفسهها پیشبینی کند. ضمن این که مدیریت موجودی انبارها، یکی از موضوعات مهم در برنامهریزی و کنترل تولید است که بحث مفصلی میطلبد. اما در این درس، تمرکزمان روی موضوعاتی است که کاربرد بیشتری در تعیین محل قرارگیری انبارها و لیاوت آنها دارند. بدین منظور، در حد کلیّات به سؤالات زیر پاسخ خواهیم داد:
چه انبارهایی ممکن است در یک کارخانه وجود داشته باشد؟ (انواع انبارها)
چه موادی و با چه مقداری در انبارها ذخیره میشوند؟ (موجودیها و کنترل موجودی)
انبارها از چه اجزای مهمی تشکیل میشوند؟
چگونه چیدمان اجزای داخلی انبارها و فضای مورد نیازشان را تعیین کنیم؟
انواع انبارها
ملاکهای متفاوتی برای طبقهبندی انبارها وجود دارد که هر کدام در جای خود مهم هستند. مثلاً انبارها را بر اساس ملاحظات مربوط به ذخیرهی مواد میتوانیم به انواع زیر تقسیم کنیم. البته گروههای دیگری هم میتوانیم به فهرست اضافه کنیم.
مواد محترقه
مواد فاسدشدنی
مواد سمی
محصولات کشاورزی
مواد فلهای
سوخت مایع
مواد خورنده
کالاهای قیمتی
انبارها را میتوانیم بر اساس محصور بودن به گروههای زیر تقسیم کنیم:
انبارهای سرباز و غیر مسقف
انبارهایی که در فضای باز هستند اما دورشان با دیوار محصور نیست (هانگارد)
انبارهای محصور و سرپوشیده
پس باید این نکته را در نظر بگیریم که فضاهای باز کارخانه هم میتوانند گزینهای برای انبار باشند، به شرطیکه مواد آن به عواملی مثل رطوبت و نور حساس نباشند.
سطح اتوماسیون میتواند ملاک دیگری برای طبقهبندی انبارها باشد:
انبارهای تمام اتوماتیک
انبارهای اتوماتیک
انبارهای نیمهاتوماتیک
انبارهای سنتی
یکی دیگر از معبارهای طبقهبندی، نوع موجودی است:
مواد اولیّه (مثل مواد خام و قطعات آمادهی خریداری شده)
محصولات نهایی
قطعات نیمساخته
سایر انبارها مثل منابع اداری (مثلاً میز، کارتریجهای پرینتر و خودکار)، منابع پشتیبانی (مثلاً قطعات مصرفی ماشینآلات و تجهیزات اندازهگیری) و منابع آبدارخانه (مثلاً مواد شوینده، چای، مایع دستشویی و دستمال)
در مورد هر کدام از این نوع انبارها، ملاحظات خاصی وجود دارد، اما ملاحظاتی که در این درس میگوییم، برای عموم آنها به کار میآید. ضمن این که معمولاً در کارخانجات: انبارهای مواد اولیه، نیمساخته و نهایی اهمیت ویژهای دارند؛ زیرا بخش زیادی از هزینهها مربوط به آنهاست و تأثیر زیادی در عملکرد کارخانه دارند.
هزینههای انبارداری
معمولاً مهمترین هزینههای انبارداری عبارتند از:
۱- هزینهی مربوط به فضا و تسهیلات موجود در انبار
بزرگتر شدن فضای انبار و استفاده از تجهیزات و ابزارهای بیشتر باعث افزایش هزینههای مربوط به: تهیهی فضا، تهیهی تجهیزات، سرویسهای تعمیر و نگهداری، دستمزد کارگران و مصرف انرژی میشود. بعضی از این موارد را جداگانه نیز بررسی خواهیم کرد.
۲- نیروی انسانی
معمولاً برای حراست از انبارها، ورود و خروج مواد، کنترل موجودیها و حفظ شرایط مناسب از نیروی انسانی استفاده میشود. معمولاً هر چه انبارها بزرگتر و مقدار موجودیها بیشتر باشد، هزینههای نیروی انسانی نیز افزایش مییابد.
۳- هزینههای مربوط به مصرف انرژی
در تمام انبارها برای روشنایی و جابهجایی مواد به انرژی نیاز است، مخصوصاً در مواردی که نگهداری مواد به شرایط ویژهای مثل کنترل دما، رطوبت یا گرد و غبار نیاز دارد.
۴- مفقود شدن یا آسیب دیدن مواد
هر چقدر هم که شرایط انبارداری ایدهآل باشد، ممکن است بعضی مواد مفقود شوند، آسیب ببینند یا فاسد شوند. این موارد نیز از هزینههای انبارداری هستند.
۵- سرمایهی راکد
اقلامی که در انبار ذخیره میشوند نوعی سرمایهی راکد هستند که با آنها کاری انجام نمیشود و سودی ندارند. حال آن که اگر سرمایهای که صرف تهیه آنها شده در بانک گذاشته شود یا در کار دیگری سرمایهگذاری شود، به آن سود تعلق میگیرد.بنابراین فرصتهای سرمایهگذاری از دست رفته هم باید به عنوان هزینه در نظر بگیریم.
۶- بیمه
گاهی بعضی اقلام موجود در انبارها بیمه میشوند یا متداول است که خود انبار برای موضوعات مثل آتشسوزی و سرقت بیمه شود. در این موارد، مبلغی که برای بیمه پرداخت میشود نیز از هزینههای انبارداری است.
۷- مالیات
مطابق قوانین مالیاتی بسیاری از کشورها به موجودی انبارها مالیات تعلق میگیرد که در اینصورت باید به هزینههای انبارداری اضافه شود.
موجودیها
سیاستهای کنترل موجودی روی موقعیت و لیاوت انبارها مؤثرند. البته معمولاً طراح کارخانه درگیر برنامهریزی و کنترل تولید نمیشود، اما باید درک درستی از موجودیها داشته باشد تا خواستههای مدیران تولید را بفهمد و در طرحهای خود لحاظ کند.
موجودی چیست؟
معنای موجودی (Inventory) در کاربردها و صنایع مختلف فرق میکند، اما عموماً به تمام چیزهایی گفته میشود که یک سازمان نگهداری میکند تا آنها را بفروشد، برای تولید استفاده کند یا از هر راه دیگری به مصرف برساند. البته موجودی باید لزوماً برای مصرف یا عرضه باشد، از این رو اقلامی مثل ماشینآلات و ابزارها حتی اگر در انبارها قرار بگیرند، موجودی به حساب نمیآیند.
انواع موجودی در کارخانه
در یک تقسیمبندی کلی میتوانیم موجودیها را به دو گروه مستقیم و غیرمستقیم تقسیم کنیم. موجودیهای مستقیم برای تولید محصول نهایی هستند و آثارشان را در محصول میبینیم، مثل فولادی که برای ساختن سیلندر از آن استفاده میشود. سایر موجودیها غیرمستقیم هستند. مثلاً تیغهی تراشکاری و آب صابون برای تولید محصول لازم هستند، اما چون مستقیماً به جزئی از محصول نهایی تبدیل نمیشوند، موجودی غیرمستقیم به حساب میآیند.
موجودیهای مستقیم را میتوانیم به مواد اولیه (Raw Material)، در جریان کار (Work in Process) و محصولات نهایی (Finished Products) طبقهبندی کنیم.
مواد اولیه اقلامی هستند که به صورت آماده تأمین میکنیم و فرقی هم ندارد که خام یا پردازششده باشند. مثلاً میتوانیم آبلیمو و شکر را بهعنوان مواد اولیه بخریم و لیموناد تولید کنیم یا خیلی از سازندگان تلفن همراه، قطعاتی مثل السیدی یا سوکت شارژر را بهعنوان مادهی اولیه خریداری میکنند.
مواد در جریان کار یا WIP اقلامی هستند که بخشی از عملیات روی آنها انجام شده اما بخش دیگر مانده است، مثل قطعهای که ماشینکاری شده اما پرداختکاری نشده است. گاهی مواد در جریان کار را ار مواد آماده مونتاژ تفکیک میکنند. در این حالت اگر تمام عملیات باقیمانده مربوط به مونتاژ باشند، ماده را آماده مونتاژ مینامند. اما اگر عملیات دیگری هم وجود داشته باشد -که مربوط به مونتاژ نباشد- به آن ماده در جریان کار میگویند. البته این تفکیک همیشه اتفاق نمیافتد و خیلی وقتها مواد آماده مونتاژ را نیز جزئی از مواد در جریان کار به شمار میآورند.
محصولات نهایی به موجودیهایی گفته میشود که آمادهی تحویل هستند.
موجودیهای غیرمستقیم را نیز میتوانیم به گروههای کوچکتر تقسیم کنیم. مثلاً اقلامی مثل روانکارها، گریس، چسب، حاملهای انرژی و قطعات مصرفی را در گروهی با عنوان «اقلام مصرفی فرایند تولید» قرار دهیم. اقلامی مثل مثل کارتریج، پوشه، خودکار و کاغذ را «اقلام اداری» بنامیم. به همین شکل گروههای دیگر برای اقلام بهداشتی، اقلام خوراکی، اقلام ایمنی و امثالهم تعریف کنیم.
مروری بر مفاهیم کلیدی مربوط به کنترل موجودی
فرض کنید سه قطعه A و B و C را بهصورت آماده خریداری کردهایم تا با مونتاژشان روزانه ۱۰۰ واحد محصول تولید کنیم. پس روزانه به صد قطعه A و B و C نیاز داریم. اما به مقداری از آنها که در کارخانه موجود است، موجودی در دسترس میگوییم.
اگر موجودی در دسترس به صفر برسد، تولید متوقف میشود و ماشینآلات و نفرات بیکار میمانند، پس وقتی موجودیها به کمتر از حد مشخصی رسید باید برای سفارش مجدد اقدام کنیم تا با کسری مواجه نشویم. به این حد مشخص، اصطلاحاً نقطهی سفارش مجدد میگوییم. ضمناً از لحظهی سفارش مواد تا دریافتشان، مدتی سپری میشود که باید در محاسباتمان لحاظ کنیم. به این مدت، زمان تحویل سفارش میگوییم.
علاوه بر این، ظرفیت تولید همیشه ۱۰۰ قطعه در روز نیست و شاید در بعضی دورههای زمانی تغییر کند. معمولاً ظرفیت تولید، تولرانس مشخصی دارد و کمترین و بیشترین مقدار آن مشخص است. اگر حدأقل تولید روزانه ۸۰ واحد باشد یعنی حدأقل نرخ مصرف قطعات A و B و C برابر با ۸۰ قطعه در روز است و اگر حدأکثر تولید ۱۲۰ قطعه باشد یعنی حدأکثر نرخ مصرف این قطعات برابر ۱۲۰ قطعه است.
ناگفته نماند که منطقی است همیشه مقداری موجودی ذخیره داشته باشیم تا اگر نرخ تولید بیشتر شد یا تحویل سفارش طول کشید با کسری روبهرو نشویم و انعطافپذیر باشیم.
برنامهریزان تولید تلاش میکنند که بهترین نقطهی سفارش مجدد، حجم سفارش و موجودی ذخیره را بر اساس پارامترهایی مثل: نرخ مصرف، زمان تحویل، هزینههای انبارداری و نرخ تورم برنامهریزی کنند. در نهایت سیاستی که برای موجودیها انتخاب میشود روی لیاوت کارخانه نیز تأثیر میگذارد.
مهمترین اجزای تشکیلدهنده انبارها
در این بخش، تعدادی از مهمترین اجزای تشکیل دهنده انبارها را بررسی میکنیم.
۱- حاملها
مواد برای این که جابهجا شوند معمولاً در حاملهایی مثل کارتنها، ظرفها، سبدها، جعبههای چوبی و پلاستیکی، پالتها و کیسهها قرار میگیرند. این حاملها جزء اجزای انبارها به حساب میآیند و باید در مورد محل قرار گیری و فضای مورد نیازشان برنامهریزی کنیم.
۲- تجهیزات استقرار مواد
منظور از تجهیرات استقرار مواد، ابزارهایی مثل قفسهها و رکها هستند که مواد روی آنها قرار میگیرند. در ادامه با چند نمونه از پرکاربردترین آنها آشنا میشوید.
قفسهها (Shelves)
قفسهها اصولاً برای استقرار اقلام کوچک و سبک هستند و معمولاً طوری طراحی میشوند که طول هر جایگاه زیاد، اما عمق و ارتفاع آن کم است.
قفسههای چرخدار (Rolling Shelves)
این قفسهها چرخ دارند و جابهجایی آنها ساده است. پس گزینهی خوبی برای انبارهای کوچک هستند تا بتوان بهتر از فضای محدودشان استفاده کرد.
رَک (Rack)
رکها بزرگتر و محکمتر از قفسهها هستند. در تصویر زیر مشاهده میکنید که کارتنها روی پالتهای چوبی قرار دارند و روی طبقات رکها مستقر شدهاند.
رک با عمق دو برابر (Double Deep Pallet Racks)
عمق این رکها بیشتر است تا پذیرای پالتها یا محمولههای بزرگتر و بیشتری باشند. معمولاً این رکها طوری طراحی میشوند که بتوان از هر دو سمت به طبقاتشان دسترسی داشت. بنابراین بهتر است کنار دیوار قرار نگیرند تا دسترسی به یک سمت محدود نشود.
رکهای متحرک (Portable Racks)
با توجه به این که معمولاً محمولههای سنگینی روی رکها قرار میگیرند، به ندرت آنها را چرخدار میسازند. با این وجود رکهای متحرک از جمله رکهای چرخدار و رکهای ریلی نیز گاهاً مورد استفاده قرار میگیرند. برای بهرهبرداری از این رکها باید حتماً به حدأکثر وزن محمولهها توجه کرد تا آسیبی به چرخها یا ریلها وارد نشود.
دراورها (Drawer Storage Units)
مجموعهای از چند کشو در ستونها و ردیفهای مختلف هستند که معمولاً برای نگهداری اقلام کوچک مثل پیچ، مهره، پین و واشر مورد استفاده قرار میگیرند.
نیمطبقهها (Mezzanines)
نیمطبقهها کمک میکنند تا فضای بیشتری در انبارها ایجاد کنیم، مثلاً بالای قفسهها یک نیمطبقه قرار میدهیم و بخشی از اقلام را در آنجا انبار کنیم.
۳- تجهیزات جابهجایی مواد
برای جابهجایی محمولهها به تجهیزات نیاز است. این تجهیزات، در بخشهای دیگر مثل واحدهای ارسال و دریافت نیز کارایی دارند.
گاریهای سرویس و نگهداری
گاریها معمولاً به پرسنل خدماتی کارخانه خدمترسانی میکنند تا بتوانند مجموعهای از ابزارها را از نقطهای به نقطهی دیگر منتقل کنند و هیچ ابزار مهمی جا نماند.
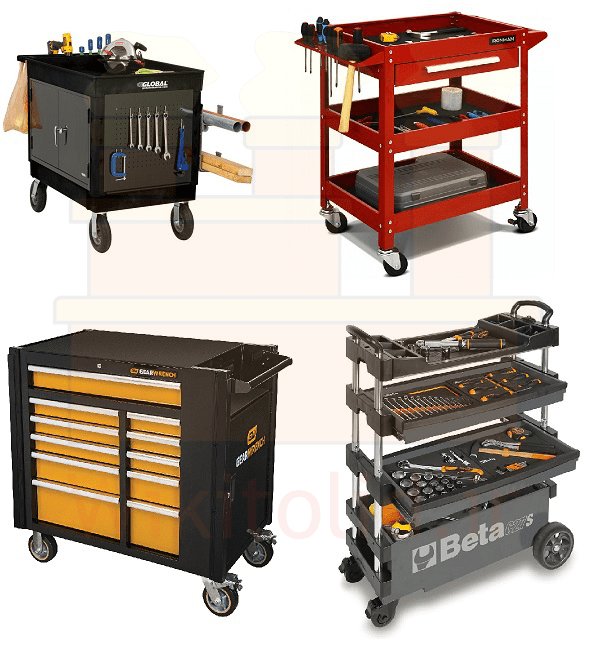
گاریهای دستی چهار چرخ
گاریهای چهارچرخ دستی ابزار ارزان قیمتی برای حملونقل اقلام سبک هستند که بیشتر در بخشهای دریافت و تحویل و انبارها استفاده میشوند.
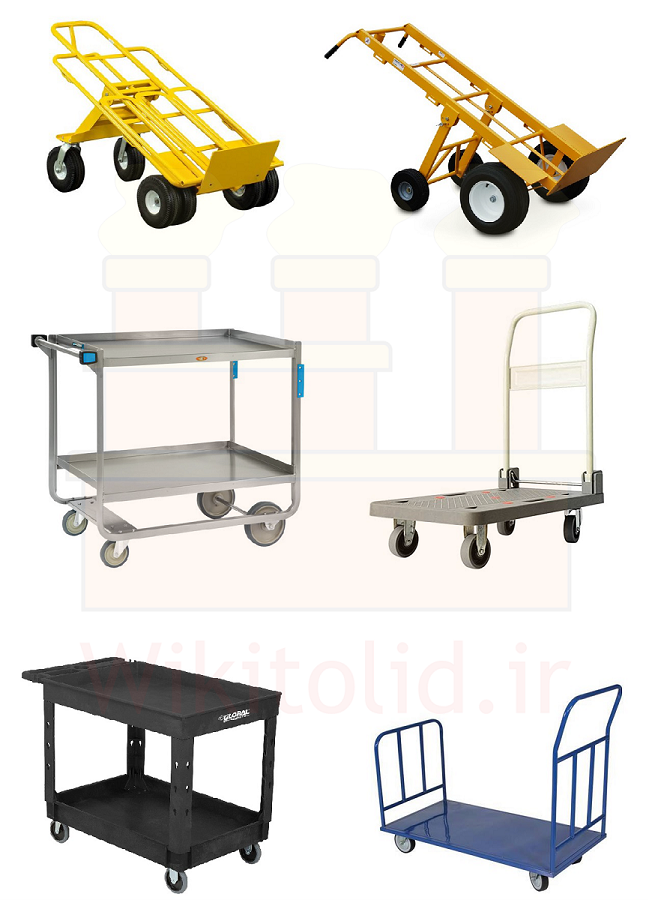
تراکهای دستی دو چرخ (Two Wheels Hand Truck)
این تراکها علاوه بر انبارها و بخشهای ارسال و دریافت ممکن است در بخشهای دیگر هم مورد استفاده قرار بگیرند و دو چرخ بودن آنها باعث میشود که قابلیت بیشتری برای چرخش و بارگیری داشته باشند.
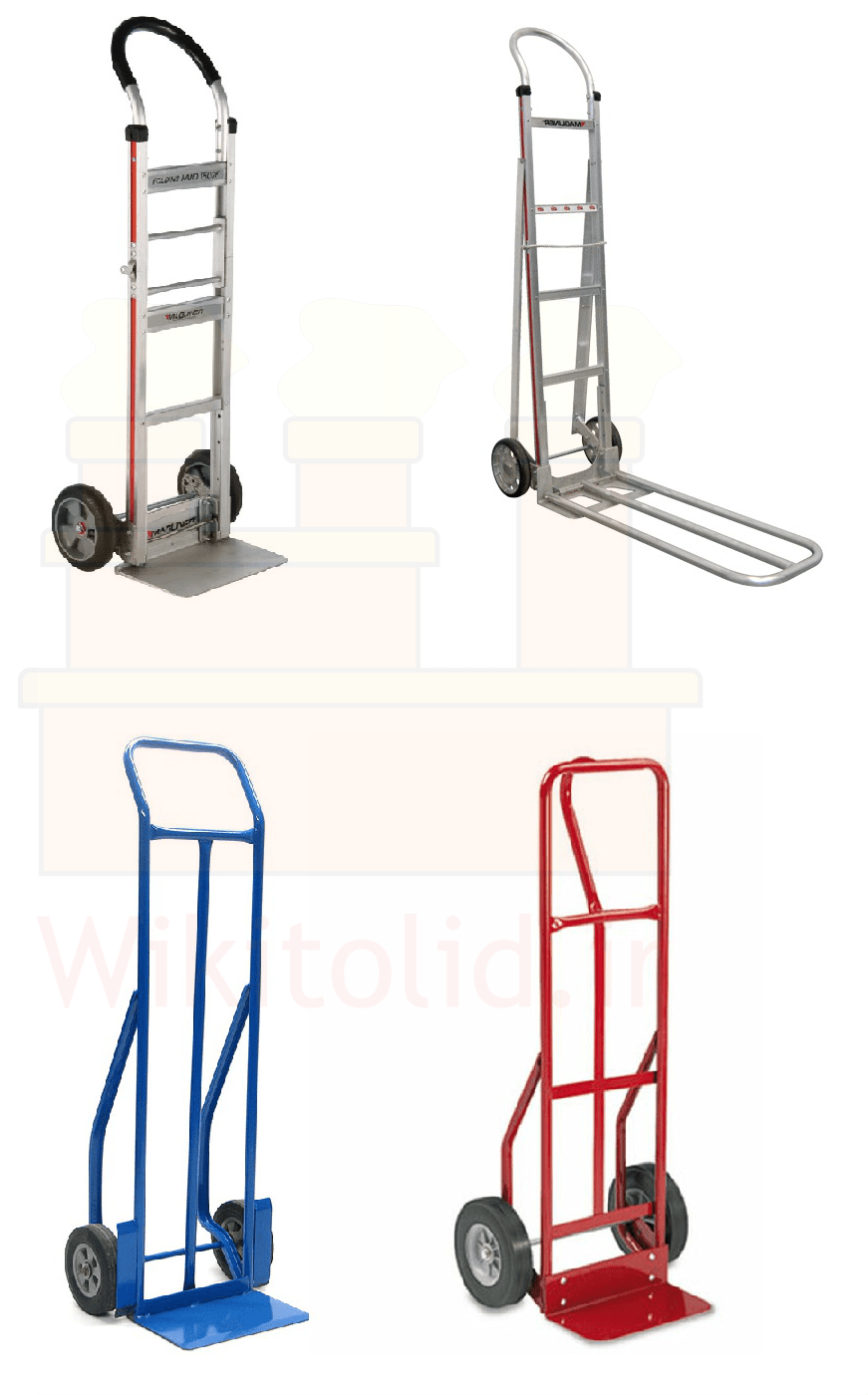
پالت تراکها (Pallet Trucks)
این ماشینها ممکن است از نوع دستی یا برقی باشند و برای جابجایی کالاهای مختلف علیالخصوص پالتها کارایی دارند که در انواع مختلف معمولی، شیبدار، ترازو دار، قیچی و امثالهم عرضه میشوند. در تصاویر زیر نمونههایی از پالتتراکتهای دستی را مشاهده میکنید.
در تصاویر زیر نمونههایی از پالتتراکهای الکتریکی را مشاهده میکنید:
ریچ تراکها (Reach Trucks)
این ماشینها برای دسترسی به طبقات فوقانی رکها هستند چون چنگالهای آن قابلیت حرکت در راستای ارتفاع را دارند و ضمناً بعضی از آنها بازویی با قابلیت در راستای طولی را دارند تا کنترل بیشتری روی پالتها و محمولهها وجود داشته باشد.
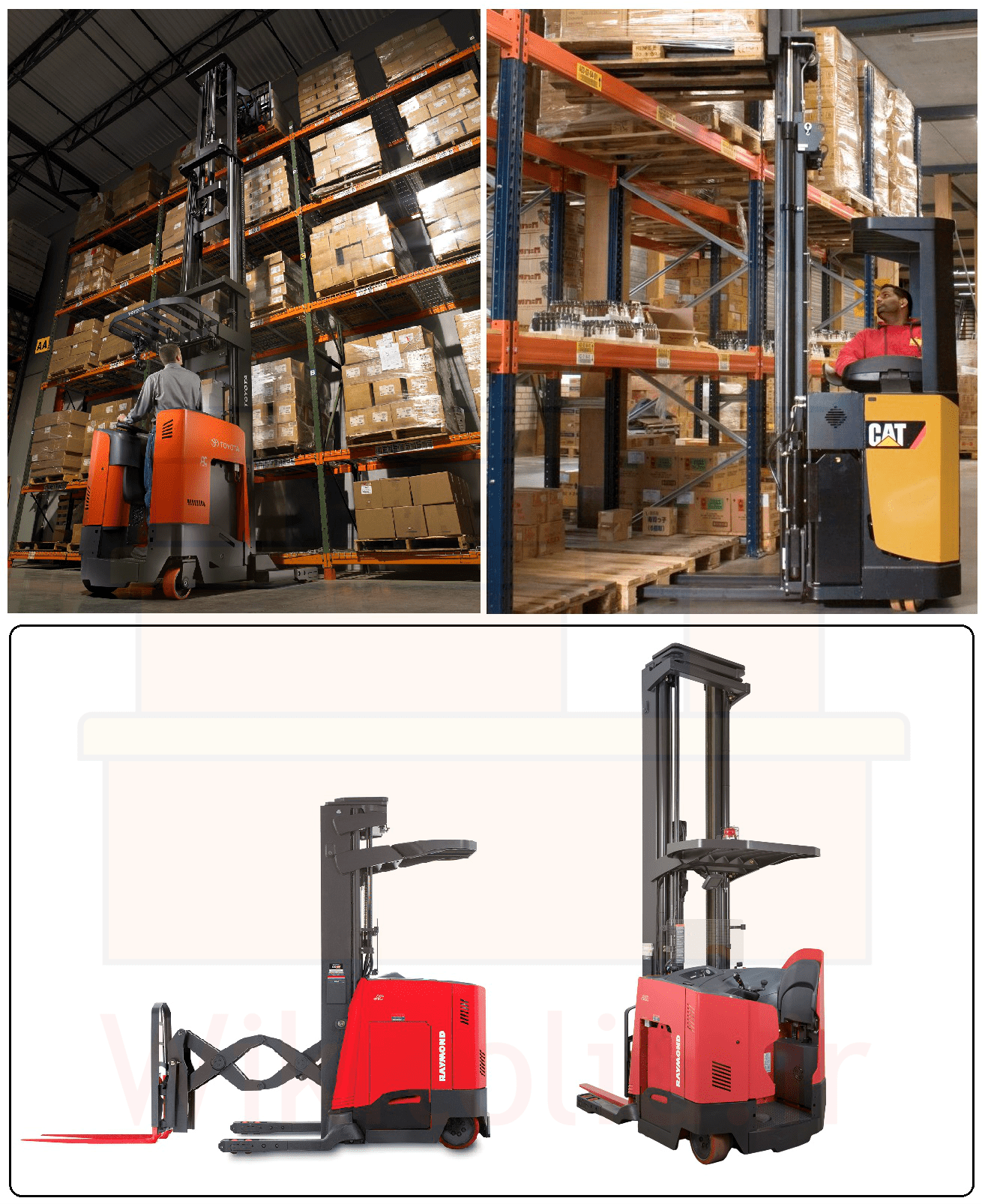
تراک برای راهروهای باریک (Very Narrow Aisle Truck)
این ماشینآلات بهطور ویژه برای راهروهای باریک طراحی شدهاند تا بدون نیاز به چرخش بتوانند از ناحیهی کناری بارگیری کنند و نیازی به چرخیدن نداشته باشند، از طرفی این ماشینآلات طرحها و کارکردهای مختلفی دارند، مثلاً بعضی از آنها برای ارتفاع زیاد در حد چند متر و بعضیهای دیگر برای ارتفاع پایینتر طراحی شدهاند.
استرادل تراک (Straddle Truck)
این تجهیزات برای بارهای سبکتر و ارتفاع کمتر مورد استفاده قرار میگیرند و در دو نوع دستی و برقی عرضه میشوند. قیمت پایین این تجهیزات به نسبت سایر تراکها و کارایی زیادشان باعث شده است که کاربرد زیادی در اغلب انبارها داشته باشند.
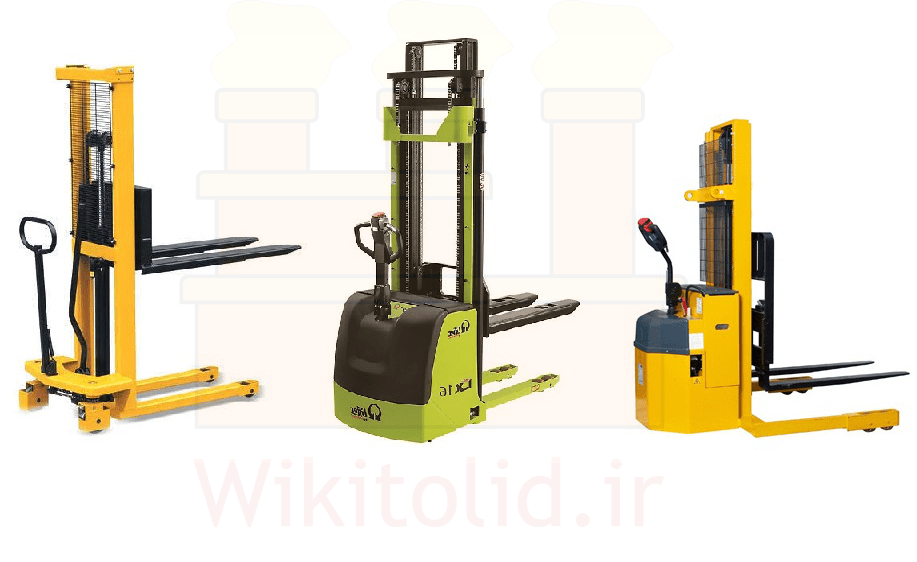
فضای مورد نیاز و لیاوت انبار
جهت برآورد کردن فضای مورد نیاز برای انبارها، میتوانیم به ترتیب زیر عمل کنیم:
۱- بررسی کنیم که چه اقلامی و با چه ابعاد و وزنی در انبار ذخیره میشوند.
۲- بررسی کنیم که بر اساس برنامههای کنترل موجودی، چه مقداری از هر ماده در انبار ذخیره میشود. سیتای سیس یتسای ستیاس یستیاس تیاس یتسیاسیسی
۳- مشخص کنیم که کدام مواد باید روی حاملها قرار بگیرند. نوع حاملها را نیز مشخص کنیم.
۴- مشخص کنیم که مواد مختلف و حاملها روی چه تجهیزاتی و با چه شکلی در کنار هم مستقر میشوند.
۵- مشخص کنیم که المانهای انبار چگونه در کنار هم قرار بگیرند.
۶- مشخص کنیم که عرض راهروها چقدر باشد.
۷- با کمک طرحی که به دست میآید، فضای مورد برای انبار را تخمین بزنیم.
در ادامه یک مثال را حل میکنیم. برای مراحل اول تا سوم میتوانیم از کاربرگی شبیه زیر استفاده کنیم. در این مثال برای استقرار مواد از قفسه و رک استفاده میکنیم. در جدول برای هر ماده مشخص شده که در قفسه قرار بگیرد یا رکها و همچنین مشخص شده که به چه تعداد جایگاه در قفسه یا رکها نیاز دارد. لازم به ذکر است برای محاسبهی تعداد جایگاه مورد نیاز باید فضای خالی بین مواد را نیز در نظر بگیریم. به عبارتی قرار نیست همه چیز را آنقدر فشرده کنیم که قرارگیری و خروج مواد دشوار شود.
برای تعیین چیدمان اجزای انبار میتوانیم از روشهایی که در طرحریزی گفتیم استفاده کنیم، مثلاً وابستگی المانها را بر اساس شدت جریان مواد بسنجیم و المانهای وابسته را نزدیک هم مستقر کنیم.
در زیر، طرح پیشنهادی برای لیاوت انبار را مشاهده میکنید. عرض راهروها را باید طوری انتخاب کنیم که برای جابهجایی بزرگترین محمولهها و تجهیرات کافی باشد. مثلاً ماشینهای VNA از بغل بارگیری میکنند و لازم نیست بچرخند. پس در صورت استفاده از آنها همین که پهنای راهرو کمی بیشتر از عرض ماشین و بزرگترین محموله باشد کافی است. اما اگر از ماشین دیگری استفاده کنیم که از جلو بارگیری میکند، باید فضای چرخیدن آن را نیز در نظر بگیریم. همچنین اگر اپراتور برای بارگیری در سمت دیگر ماشین میایستد، باید حدود ۵۰ الی ۶۰ سانتیمتر به پهنای راهرو اضافه کنیم.
دیدگاه خود را ثبت کنید
تمایل دارید در گفتگوها شرکت کنید؟در گفتگو ها شرکت کنید.