شما در حال خواندن درس استقرار بر اساس تکنولوژی گروهی هستید. این درس مربوط به مجموعه طرحریزی است.
در درسهای گذشته با انواع «استقرار محصولی» و «استقرار فرایندی» آشنا شدید. گاهی برای چیدمان تسهیلات، از ترکیب این دو چیدمان استفاده میشود که اصطلاحاً به آن «استقرار ترکیبی» میگوییم. برای پیادهسازی استقرار ترکیبی، از روشهای مختلفی میتوان استفاده کرد که یکی از آنها تکنولوژی گروهی یا Group Technology (به اختصار GT) است. در این روش با گروهبندی قطعات و محصولاتی که در یک واحد تولیدی ساخته میشوند، نحوهی قرارگیری ماشینآلات و سایر تسهیلات تعیین میشود. در ویکیتولید، این روش را به عنوان یک مصداق و صرفاً برای درک بهتر استقرار ترکیبی ارائه خواهیم کرد.
برای این که بتوانید یک تصویر اولیه از تکنولوژی گروهی داشته باشید، فرض کنید یک کارگاه از ده دستگاه تشکیل شده است. در تصویر زیر، این دستگاهها را با اعداد ۱ تا ۱۰ شمارهگذاری کردهایم. همچنین در این کارگاه ده محصول مختلف ساخته میشود که آنها را با حروف انگلیسی (مثل A و B و C) نامگذاری کردهایم. در حالت عادی، اگر از استقرار فرایندی استفاده کنیم، احتمالاً مسیر عبور قطعات از میان دستگاهها شبیه تصویر زیر است. در این وضعیت، مسافت و زمان جابهجایی مواد نسبتاً زیاد است که باعث افزایش هزینهها میشود.
اگر در کارگاه بالا، چیدمان قرارگیری تسهیلات را با کمک تکنولوژی گروهی تنظیم کنیم، مسیر جابهجایی مواد برای تولید هر محصول -مثل محصول A یا B- به شکل زیر اصلاح میشود. در این وضعیت جدید، هزینهها کاهش و بهرهوری افزایش مییابد. اگر بخواهیم بر اساس این دو تصویر تأثیر تکنولوژی گروهی را شناسایی کنیم، در وضعیت جدید: ماشینآلات به سه گروه تقسیم شدهاند که گروه اول (شامل ماشینهای ۲ و ۴ و ۵) برای قطعات A و B، گروه دوم (ماشینهای ۱ و ۳ و ۵ و ۷) برای قطعات C و D و E و F و گروه سوم (ماشینهای ۶ و ۸ و ۹ و ۱۰) برای قطعات G و H و I و J است. این چیدمان در اصل با کمک «گروهبندی قطعات» انتخاب شده که روش آن را در این درس یاد میگیرید.
مراحل پیادهسازی تکنولوژی گروهی
اگر تکنولوژی گروهی را صرفاً ناظر بر چیدمان ماشینآلات بدانیم، پیادهسازی آن به سه مرحلهی زیر تقسیم میشود.
۱- فهرست کردن قطعات و کدگذاری
کُد گذاری قطعات موضوعی نیست که فقط متعلق به تکنولوژی گروهی باشد، بلکه به صورت کلّی اقدامی مفید برای طبقهبندی و مدیریت بهتر قطعات است. معیارها مختلفی برای کد گذاری قطعات وجود دارد، مثلاً میتوان آنها را بر اساس شکل، مادهی سازنده، روش ساخت، ابعاد، کاربردشان، یا ترکیبی از این موارد کدگذاری کرد. همچنین استانداردهای مختلفی برای کدگذاری وجود دارد، مثلاً شاید مطابق یک استاندارد، قطعات فولادی با حرف S و مطابق استانداردی دیگر با حرف St نشان دهند.
در مورد پیادهسازی تکنولوژی گروهی، فارغ از اثرات مثبت کد گذاری، باید فهرست محصولات و قطعات را مشخص کنیم. به عبارت دیگر، تا وقتی ندانیم که چه محصولات و قطعاتی قرار است توسط ماشینآلات تولید شود، امکان پیادهسازی این روش مقدور نیست. در مورد کد گذاری، با این که بسیاری از منابع روش Optiz را پیشنهاد کردهاند، استاندارد واحد و مشخصی برای پیادهسازی تکنولوژی گروهی وجود ندارد و حسب مورد میتوانیم از استانداردهای متفاوتی استفاده کنیم.
۲- گروهبندی قطعات و گروهبندی ماشینآلات
در این مرحله، قطعات یا محصولاتی که در مرحلهی اول فهرست کردهایم باید به چند گروه یا اصطلاحاً خانواده تقسیم شوند. در تصویر بالا، قطعات A و B هر دو توسط ماشینهای ۲ و ۴ و ۵ ساخته میشوند و توالی عملیات مشابهی دارند، یعنی به ترتیب از ماشینهای ۲ و ۴ و ۵ عبور میکنند، به همین علت آنها را عضو یک گروه یا خانوادهی مشترک فرض کردیم. برای تشکیل خانوادههای قطعات، معیارهای متفاوتی وجود دارد که در ادامه به تعدادی از آنها اشاره میکنیم:
شکل قطعات: مثلاً قطعات متقارن را میتوانیم با دستگاه تراش ماشینکاری کنیم اما قطعات نامتقارن به تجهیزاتی مثل دستگاه فرز نیاز دارند. بنابراین اگر شکل بعضی قطعات باعث میشود که به تجهیزات خاصی نیاز داشته باشند، میتوانیم آنها را در گروهی یکسان قرار دهیم.
ابعاد قطعات: مثلاً دهانهی ورودی فرز CNC یا طول دستگاههای تراش و قطر ورودی اسپیندل محدود است و گاهی برای قطعات سنگین باید از تجهیزات جداگانهای استفاده کنیم. به همین علت میتوانیم بعضی قطعات را صرفاً به دلیل ابعاد مشابه، در یک گروه قرار دهیم.
وزن قطعات: به عنوان مثال، میزان تحمل اسپیندلهای تراشکاری و جرثقیلهای سقفی محدود است؛ بنابراین شاید بهتر باشد قطعات سنگین را در گروه مجزایی قرار دهیم تا از تجهیزات خاصی برای آنها استفاده شود.
جنس قطعات: به عنوان مثال، ماشینکاری یک قطعهی سخت چدنی به ابزار متفاوتی نسبت به یک قطعهی آلومینیومی نیاز دارد. بدین جهت، گاهاً جنس مواد یکی از معیارهای مهم در شناسایی تجهیزات مناسب است.
مهارت مورد نیاز برای ساخت: گاهاً ساخت بعضی قطعات به مهارتهای مشابهی نیاز دارد و لذا میتوانیم آنها را در گروهی یکسان قرار دهیم تا نفرات مشترکی روی آنها کار کنند.
ظرفیت تولید: ظرفیت تولید ماشینآلات متفاوت دارند؛ لذا مقدار تولید هر قطعه میتواند معیار مهمی در انتخاب تجهیزات مناسب باشد. بدین جهت گاهاً مفید است که قطعات بر اساس مقدار تولیدشان در یک گروه قرار بگیرند.
دقت ساخت: دقت فرایندها و تجهیزات مختلف در ساخت قطعات متفاوت است. از این رو گاهی بعضی قطعات با دقت مشابه را در گروهی یکسان قرار میدهیم تا از تجهیرات مشترکی برای آنها استفاده شود.
روش تولید: با اینکه موارد قبلی روی انتخاب روش تولید موثر هستند اما میتوانیم مستقیماً فرایند تولید قطعات را برای کشف موارد مشابه بررسی کنیم.
اقدام دیگر، گروهبندی تجهیزات است. در تصویر بالا، دستگاههای ۲ و ۴ و ۵ فقط برای تولید قطعات A و B کارایی دارند، پس آنها را اعضای یک گروه مستقل در نظر گرفتیم. اصطلاحاً به گروههای ماشینآلات و تجهیزات سلول ساخت (Manufacturing Cell) گفته میشود. این گروهها یا سلولها لزوماً متشکل از چند دستگاه مختلف نیستند و شاید فقط یک دستگاه، مثلاً یک دستگاه تراش، در آنها مستقر باشد. همچنین تمام تجهیزاتی که در این سلولها قرار میگیرند لزوماً برای پردازش مواد و ساخت محصول نیستند، مثلاً شاید یک سلول علاوه بر تجهیزات تولیدی (مثل دستگاه فرز) شامل یک دستگاه آزمایشگاهی (مثل سختیسنج) و یک دستگاه حملونقل مواد (مثل جرثقیل) نیز باشد. به عنوان یک قاعدهی سرانگشتی و نه چندان دقیق، در بعضی منابع توصیه شده است که تعداد تجهیزات مستقر در سلولها، نباید بیشتر از ۵ عدد باشد.
روشهای مختلفی برای تعیین تچهیزات مستقر در هر سلول ساخت وجود دارد که در منابع مختلف به آنها اشاره شده است. در این درس، به عنوان نمونه از الگوریتم کینگ (Kings Algorithm) استفاده میکنیم.
استفاده از الگوریتم مرتبسازی باینری یا کینگ
در این روش، ابتدا ماتریسی شامل فهرست قطعات و ماشینآلات تهیه میکنیم. در این ماتریس باید مشخص کنیم که ساخت هر قطعه به کدام تجهیزات نیاز دارد، مثلاً در جدول زیر نشان دادیم که قطعهی P15 با دستگاههای M3 و M6 ساخته میشود.
در جدول بالا، به جای نقطههای سیاه عدد ۱ و در خانههای سفید عدد صفر میگذاریم. همچنین، ستونها را از راست به چپ و ردیفها را از بالا به پایین شمارهگذاری میکنیم. در جدول زیر، شمارهی سطرها و ستونها را با رنگ قرمز نشان دادیم. بدیهی است که شمارهی قطعهی P2 همان عدد ۲ و شمارهی ماشین M4 همان عدد ۴ است.
در ادامه، باید ارزش هر کدام از خانههای جدول را تعیین کنیم. برای این کار، مقدار هر خانه -که طبیعتاً صفر یا یک است- در عدد ۲n-j ضرب میکنیم. n تعداد قطعات است که مقدار ثابتی دارد و در این مثال برابر با عدد ۸ است. j شماره قطعهی مورد نظرمان، یا همان شمارهی ستون است. بدین ترتیب، مقدار اولین خانه در ردیف ۱ (مربوط به قطعه ۱ و ماشین ۱) برابر با ۱۲۸، مقدار چهارمین خانه برابر با ۱۶ و مقدار هفتمین خانه برابر ۲ است. با جمع زدن این مقادیر، ارزش ردیف اول برابر ۱۴۶ است.
اگر ارزش همهی ردیفها را محاسبه کنیم، جدول زیر به دست میآید:
در ادامه، ردیفها را به ترتیب ارزشی که برای آنها محاسبه کردیم از زیاد به کم مرتب میکنیم.
به همان شکل که ارزش هر ردیف را محاسبه کردیم، ارزش هر ستون را نیز باید محاسبه کنیم. برای این کار، مقدار هر خانه را در عدد ۲m-k ضرب میکنیم. m تعداد ماشینآلات است که مقدار ثابتی دارد و در این مثال برابر ۴ است. K شماره ماشین مورد نظرمان، یا همان شمارهی ردیف است. در پایان با جمع زدن مقادیر خانههای هر ستون، ارزش آن ستون را به دست میآوریم.
اگر ردیفها را نیز به ترتیب ارزش آنها از بالا به پایین مرتب کنیم، جدول شبیه زیر میشود:
دو مرحلهی قبلی، یعنی مرتب کردن سطرها و ستونها به ترتیب امتیار را آنقدر ادامه میدهیم تا جدول قابل تغییر نباشد. اگر برای بار دوم ردیفها را مرتب کنیم، جدول به صورت زیر تغییر میکند:
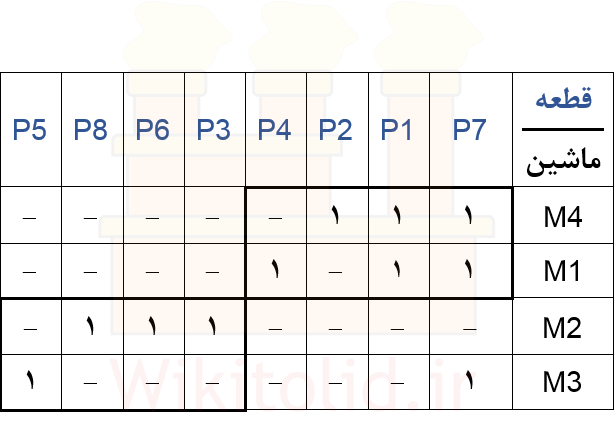
اگر بخواهیم ستونهای جدول بالا را مرتب کنیم، تغییری نمیکند. بنابراین مرتب کردن جدول را به پایان میرسانیم. مطابق جدول بالا، گروهبندی نهایی به شکل زیر است:
سلول اول شامل ماشینهای M4 و M1 که خانوادهی قطعات P7 و P1 و P2 و P4 در آن ساخته میشوند.
سلول دوم شامل ماشینهای M2 و M3 است که خانوادهی قطعات P3 و P6 و P8 و P5 در آن ساخته میشوند.
قطعهی P7 به هیچ خانوادهای تعلق ندارد.
در این مثال، قطعهی P7 در هیچ گروهی نیست و همانطور که میبینید، بخشی از فرایند تولید آن در سلول اول و بخش دیگر در سلول دوم انجام میشود. در چنین شرایطی میتوانیم یکی از راهکارهای زیر را انتخاب کنیم:
از ساختن قطعهی P7 صرفنظر و تولید آن را برونسپاری کنیم.
تجهیزات مورد نیاز برای قطعه P7 را به یکی از سلولها اضافه کنیم. به عنوان مثال، قطعه P7 را میتوانیم با اضافه کردن یک ماشین M3 به سلول اول، به همراه قطعات P1 ،P2 و P4 تولید کنیم.
میتوانیم بخشی از فرایند تولید را در یکی از سلولها انجام دهیم، سپس قطعه را به سلولهای دیگر منتقل کنیم.
۳- تعیین چیدمان ماشینآلات
تجهیرات در هر سلول (یا گروه تجهیرات) میتوانند چیدمان متفاوتی داشته باشند. همچنین سلولها نیز میتوانند آرایش متفاوتی در کنار هم داشته باشند. در تکنولوژی گروهی، سه نوع چیدمان برای سلولها و تجهیزات قابل تصور است که تصویرشان را در ادامه مشاهده میکنید؛ البته این تصاویر صرفاً الگو هستند و برای استقرار دقیقتر باید به دانش طرحریزی و مطالبی که در سایر درسهای این مجموعه ارائه میشود مسلط باشید.
چیدمان اول: خط جریان (Flow Line)
چیدمان دوم: سلول (Cell)
چیدمان سوم: مرکز (Center)
مزایا و معایب استفاده از تکنولوژی گروهی
بعضی از مهمترین مزایای استفاده از تکنولوژی گروهی عبارتند از:
معمولاً در استقرار گروهی، اعم جابهجایی مواد در فرایند تولید به محدودهی سلولها خلاصه میشود، بنابراین هزینهی حملونقل مواد کمتر از استقرار فرایندی است.
با توجه به این که هر سلول برای گروههای مشخصی از قطعات است، شرایط مساعدتری برای سفارشیسازی ماشینآلات وجود دارد. البته بدیهی است که تنوع محصولات باعث میشود شرایط بهینهسازی به اندازهی استقرار محصولی مساعد نباشد.
معمولاً در هر سلول ساخت (که متشکل از تعدادی ماشینآلات است) از کارکنان ثابت استفاده میشود. با توجه به این که قطعات مشابهی در هر سلول ساخته میشوند، این افراد سادهتر با فرایند تولید قطعات آشنا میشوند، عملکردشان بهبود مییابد، ایرادها را سادهتر شناسایی میکنند و رضایت شغلی بالاتری خواهند داشت.
بعضی از مهمترین معایب تکنولوژی گروهی عبارتند از:
گروهبندی قطعات و ماشینآلات زمانبر است، مخصوصاً وقتی قطعات قبلی تغییر میکنند یا قطعهی جدیدی اضافه میشود، گروههای قطعات و سلولهای ساخت نیاز به بازنگری و گاهاً تغییر دارند.
گروهبندی سلولها و قطعات باعث محدودیت در طراحی محصولات و فرایندها میشود، مثلاً قطعات باید طوری طراحی شوند که حتیالمقدور در یکی از گروههای موجود قرار بگیرند و بتوان آن را در یکی از سلولهای کنونی ساخت.
معمولاً فعالیت سلولها متوازن نیست و زمان بیکاری بعضی ماشینآلات زیاد است.
گاه تنوع قطعات، پیادهسازی استقرار گروهی را دشوار میکند.
دیدگاه خود را ثبت کنید
تمایل دارید در گفتگوها شرکت کنید؟در گفتگو ها شرکت کنید.