شما در حال خواندن شاخصهای پرکاربرد در ارزیابی طرحها هستید. این درس مربوط به مجموعه طرحریزی است.
در فاز سوم طرحریزی با بعضی از روشهای ارزیابی مثل مطالعهی انتقال مواد و مقایسهی هزینهها آشنا شدید. اما موضوعی که کمتر به آن پرداختیم، استفاده از شاخصهای ارزیابی است. شاخصها وضعیت یک یا چند پارامتر را نشان میدهند. البته قبلاً هم با بعضی شاخصها آشنا شدهاید. مثلاً در درس ارزیابی حملونقل از مدل مسافت گفتیم که خروجی آن نوعی شاخص است یا در درس مقایسهی هزینهها با شاخصی به نام نرخ بازگشت سرمایه آشنا شدید. اما باید این نکته را در نظر داشته باشیم که محدودیتی برای استفاده از شاخصها وجود ندارد و تحلیلگر میتواند متناسب با نیازش، از شاخصهای مختلف استفاده کند یا شاخصهای جدید تعریف کند.
شاخصهای این درس را از کتاب طرحریزی Stephen و Meyers انتخاب کردیم و نمونههای دیگری از آنها را میتوانید در کتاب جیمز اپل پیدا کنید.
شاخصهای مبتنی بر مسافت
شاخصها میتوانند بر اساس مسافت تعریف شوند. مثلاً میتوانیم بررسی کنیم که چقدر از مسافت توسط نوارنقالهها یا لیفتراک پیموده میشوند یا چند درصد از مسیرها مربوط به جابهجایی عمودی مواد (مثلاً انتقال از طبقهای به طبقهی دیگر) هستند. در ادامه با دو شاخص پرکاربرد در ارتباط با مسافت آشنا میشوید.
۱- نسبت جابهجایی خودکار (Automatic Travel Ratio)
با کمک این شاخص میخواهیم بدانیم که چند درصد از مسیرها بهصورت اتوماتیک پیموده میشوند؟ مثلاً اگر جعبهای با کمک یک نوار نقاله از بخشی به بخش دیگر منتقل شود یعنی این مسافت را بهصورت اتوماتیک طی کرده است.
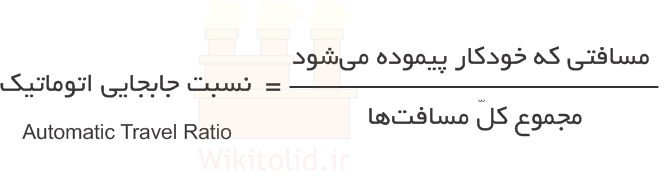
۲- شاخص استفاده از جاذبه (Gravity Ratio) در جابهجاییها
استفاده از نیروی جاذبه در جابهجاییها باعث کاهش مصرف انرژی میشود و به همین علت ترجیح میدهیم که سهم بیشتری در انتقال مواد داشته باشند و شاخص زیر میتواند یکی از ملاکهای ارزیابی آن باشد.
شاخصهایی در مورد استفاده بهینه از فضا
برای استفادهی بهتر از فضا راهکارهای مختلفی وجود دارد، مثلاً میتوانیم راهروهای باریکتری داشته باشیم یا فاصلهی ماشینآلات را کم کنیم و برای هر کدام از آنها شاخصی در نظر بگیریم تا ببینیم کدام طرح بهینهتر است.
۱- درصد راهروها (Percent of aisle space)
این شاخص نشان میدهد که چند درصد از فضای کل به راهروها اختصاص داده میشود. البته به تنهایی نمیتوان آن را ملاک خوبی برای سنجش بهینه بودن فضا دانست. چون اتفاقاً گاهی بزرگتر بودن راهروها باعث کاهش هزینههای حملونقل و افزایش بهرهوری میشود، یا شاید از فضای راهروها بعداً بتوانیم برای توسعه واحد تولیدی استفاده کنیم.
۲- درصد استفاده از فضا برای انبار
این شاخص، نشان میدهد که چه مقدار از فضا صرف انبار شدن مواد میشود. مواد فقط در انبارها انباشته نمیشوند، بلکه معمولاً مقداری ماده در کنار ایستگاههای کاری، واحد ارسال، واحد تحویل و بسیاری از بخشهای دیگر کارخانه وجود دارد. بنابراین از این شاخص میتوان برای هر بخشی از کارخانه استفاده کرد. لازم به توجه است که در رابطهی زیر، فضایی که مواد در سه بُعد اشغال میکنند -نه مساحت دو بعدی- مبنا قرار میگیرد.
۳- درصد استفادهی ماشینآلات از فضا (Machine Space Utilization)
با کمک این شاخص بررسی میکنیم که چند درصد از فضای موجود توسط ماشینآلات اشغال میشود. در رابطه زیر، مساحتی که اشغال میشود مبنا قرار گرفته است. اما در بعضی موارد خاص که از نیمطبقات و جرثقیلها استفاده شده، مناسبتر است که فضای اشغال شده را مبنا قرار دهیم.
نرخ به کارگیری ماشین
منظور از نرخ به کارگیری ماشین این است که چقدر از توان و ظرفیت آنها استفاده میشود، مثلاً میتوانیم زمان بیکاری هر ماشین را به نسبت کل زمان کاری محاسبه کنیم یا ببینیم که چند درصد از ظرفیت تولید مورد استفاده قرار میگیرد.
۱- درصد استفاده از ماشین (Percent of machine utilization)
این شاخص نشان میدهد که چقدر از ظرفیت تئوریک ماشین استفاده میشود، مثلاً شاید یک ماشین بتواند در شرایط ایدهآل ۲۰ قطعه در هر ساعت تولید کند اما با توجه به زمانی که برای ورود و خروج قطعهکار و تنظیم ماشین و بازرسی آن صرف میشود، شاید در عمل فقط ۱۲ قطعه تولید شود و نسبت این دو عدد نشان میدهد که چقدر از ظرفیت آن استفاده میکنیم. البته این شاخص الزاماً برای یک ماشین تعریف نمیشود، بلکه میتوانیم بررسی کنیم که در یک دپارتمان یا حتی کل کارخانه، مجموعاً چقدر از ظرفیت تئوریک تمام ماشینآلات یا گروه خاصی از آنها (مثلا ماشینآلات بستهبندی) استفاده میشود.
۲- درصد ماشینهایی با بارگذاری اتوماتیک (Percent of automatic loading machine)
قراردادن قطعه کار در دستگاه میتواند زمان زیادی را صرف کند و گاهی با اتوماتیک کردن آن میتوانیم ظرفیت واقعی تولید را تا چند برابر افزایش دهیم. به همین علت میتوانیم با شاخص زیر بررسی کنیم که چند درصد ماشینآلات از ورود اتوماتیک مواد پشتیبانی میکنند.
کنترل هزینههای مربوط به انتقال مواد
در درس ارزیابی طرحها بر اساس انتقال مواد با مدلهای مختلفی آشنا شدید که نتایج هر کدام از آنها را میتوانیم یک شاخص بدانیم. یکی دیگر از شاخصها در مورد انتقال مواد را در زیر مشاهده میکنید. این شاخص نشان میدهد که چند درصد از زمان کاری به انتقال مواد اختصاص دارد. بدیهی است هر چه این مدت زمان کوتاهتر باشد، مناسبتر است.
نسبت زمان حضور در کارخانه
برای پیادهسازی سیستم تولید به هنگام (Just in time) ترجیح میدهیم که مواد برای مدت کوتاهتری در کارخانه باشند. برای سنجش این موضوع میتوانیم از شاخص «زمان حضور در کارخانه» استفاده کنیم. ضمناً برای استفاده از شاخص زیر باید با مفهوم زمان چرخه آشنا باشید که نحوهی محاسبه آن را در درس خط تولید توضیح دادهایم.
دیدگاه خود را ثبت کنید
تمایل دارید در گفتگوها شرکت کنید؟در گفتگو ها شرکت کنید.